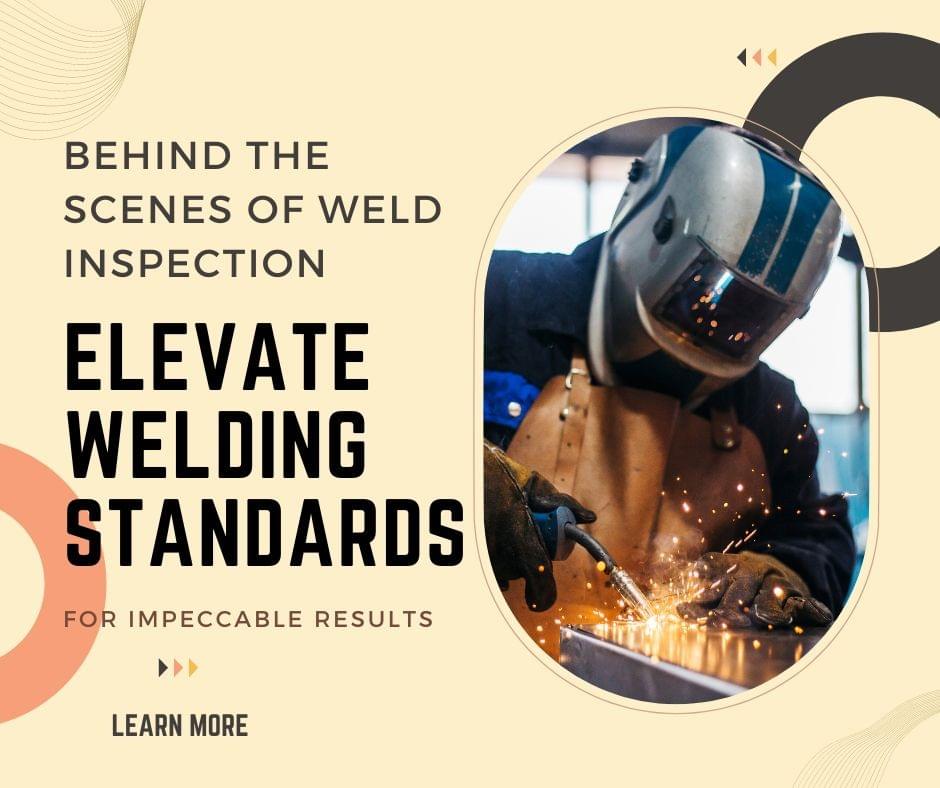
Welding, a cornerstone of construction and manufacturing, demands not only skillful craftsmanship but also meticulous inspection to ensure structural integrity and safety. Behind the scenes of every successful welding project lies a robust weld inspection process that adheres to the highest standards. In this exploration, we delve into the intricacies of weld inspection, shedding light on the methodologies that elevate welding standards to achieve impeccable results.
The Crucial Role of Weld Inspection
Weld inspection is the linchpin of quality control in welding projects. It involves a systematic examination of welds to verify compliance with specified standards, ensuring that the final product meets the required structural and safety criteria. A comprehensive inspection process is essential to identify defects, inconsistencies, or imperfections that might compromise the weld's performance.
Methods of Weld Inspection
1. Visual Inspection:
Visual inspection is the most fundamental and widely used method. It involves a detailed examination of the weld's surface for any visible defects, such as cracks, incomplete fusion, or inadequate penetration. A skilled inspector can discern imperfections that might elude the untrained eye.
2. Radiographic Testing:
Radiographic testing utilizes X-rays or gamma rays to create an image of the weld's internal structure. This method is highly effective in revealing subsurface defects, making it a cornerstone in weld inspection, especially for critical applications like aerospace and nuclear industries.
3. Ultrasonic Testing:
Ultrasonic testing involves the use of high-frequency soundwaves to detect internal flaws or inconsistencies within a weld. This method is particularly useful for assessing the thickness of welds and identifying defects like porosity and inclusions.
4. Magnetic Particle Inspection:
Magnetic Particle Inspection (MPI) is a non-destructive testing method used to identify surface and near-surface defects. It involves the application of magnetic fields and iron particles to reveal discontinuities such as cracks. While not destructive, MPI plays a crucial role in complementing other inspection techniques.
The Power of Magnetic Particle Inspection
Magnetic Particle Inspection (MPI):
MPI is a versatile and effective method for detecting surface and near-surface defects in ferrous materials. During the inspection process, the material is magnetised, and iron particles—either dry or suspended in a liquid—are applied to the surface. These particles accumulate at areas with magnetic flux leakage, highlighting defects like cracks or discontinuities.
Weld Inspection Certification:
Weld inspection professionals often undergo rigorous training to attain certification. This certification ensures that inspectors possess the necessary knowledge and skills to perform accurate and reliable inspections. The weld inspection certification process typically includes theoretical understanding, practical application, and adherence to industry standards.
Elevating Welding Standards for Impeccable Results
1. Stringent Quality Control:
Weld inspection, including methods like MPI, imposes stringent quality control measures. By identifying and addressing defects early in the welding process, the overall quality of the weld is enhanced, leading to a finished product that meets or exceeds industry standards.
2. Compliance with Industry Regulations:
Many industries have specific regulations governing welding standards, especially in sectors such as aerospace, automotive, and construction. Adhering to these regulations is not only a legal requirement but also essential for ensuring the safety and reliability of the final product.
3. Preventing Costly Failures:
Rigorous weld inspection, including techniques like MPI, is a proactive measure to prevent costly failures. Identifying and rectifying defects during the inspection phase reduces the risk of weld failure in real-world applications, saving both time and resources.
4. Continuous Improvement:
Weld inspection, when performed systematically, becomes a catalyst for continuous improvement. Insights gained from the inspection process contribute to refining welding procedures, enhancing the skills of welders, and ultimately elevating the overall standard of welding practices.
Conclusion: Illuminating the Weld Inspection Process
Behind every successful welding project is a well-executed weld inspection process. Whether through visual examination, radiographic testing, ultrasonic inspection, or the powerful Magnetic Particle Inspection, each methodplays a crucial role in ensuring the integrity and reliability of welds. Elevating welding standards through meticulous inspection not only meets regulatory requirements but also contributes to the creation of structures and products that stand the test of time.