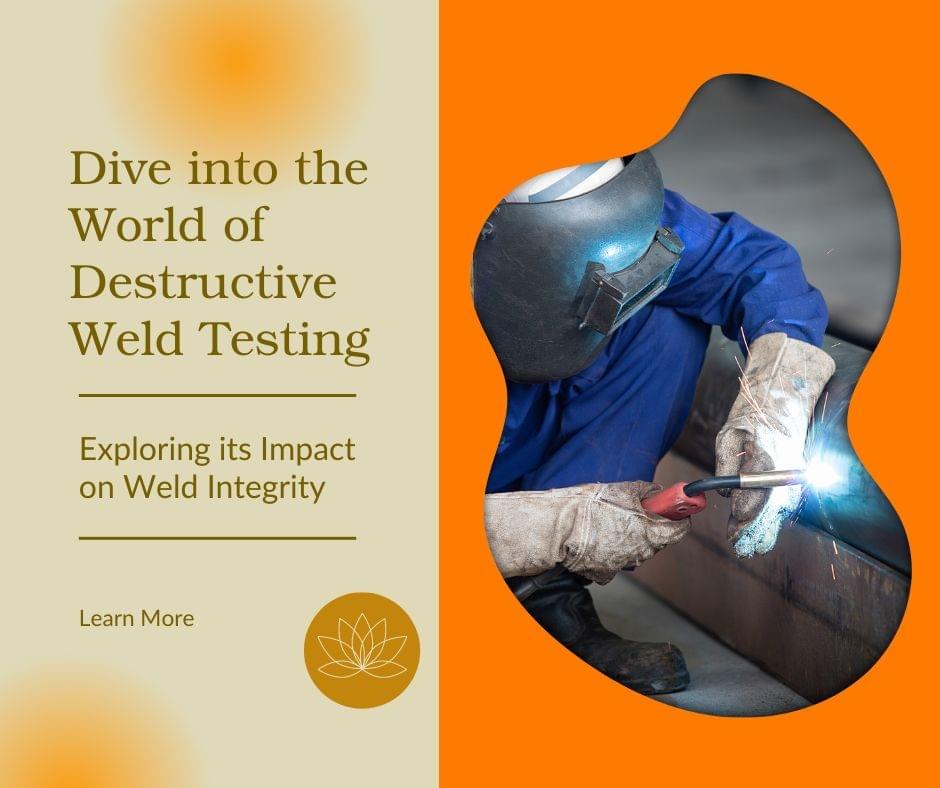
Welding, an indispensable art in the realm of metal fabrication, demands not only skillful execution but also rigorous testing to ensure weld integrity. Among the various testing methods, destructive weld testing stands out as a crucial step in evaluating the soundness of welds. In this exploration, we immerse ourselves in the world of destructive weld testing, unveiling its significance and impact on weld integrity.
Understanding Destructive Weld Testing: A Deeper Insight
The Essence of Destruction for Evaluation:
Destructive weld testing involves subjecting a weld to extreme conditions, leading to its ultimate failure. While this might seem counterintuitive, the purpose is to scrutinize the weld's performance under stress, providing insights into its structural integrity. Common methods include bend tests, tensile tests, and impact tests.
Bend Tests:
Bend tests are a common form of destructive testing that assesses the ductility and soundness of a weld. A section of the welded material is bent to a specific angle, and the result is scrutinized for signs of cracking, delamination, or other defects. This test is particularly valuable
in determining the weld's ability to withstand deformation without failure.
Significance of Destructive Testing in Evaluating Weld Integrity
Ensuring Weld Strength:
Destructive weld testing is a robust measure to evaluate the inherent strength of a weld. It helps determine the load-bearing capacity and resilience of the welded joint. This is especially critical in applications where the welds are subjected to varying degrees of stress and pressure.
Identifying Weld Defects:
Weld defects, though undesirable, are a reality in the welding process. Destructive testing brings these defects to light by inducing failure under controlled conditions. This identification is crucial for rectifying issues in the welding procedure, ensuring that subsequent welds meet
the required standards.
Impact of Destructive Testing on Weld Integrity
Certifying Weld Integrity:
For industries where weld integrity is non-negotiable, suchas aerospace, automotive, and structural engineering, destructive testing plays a pivotal role in certifying weld integrity. Meeting stringent standards is often a prerequisite, and destructive testing provides the evidence needed to assure compliance.
Enhancing Weld Procedure:
Destructive weld testing serves as a feedback mechanism for weld procedure improvement. By analyzing the failure modes and identifying weak points,
welders can refine their techniques, adjust parameters, and implement changes
that contribute to enhanced weld integrity in future endeavors.
Challenges and Best Practices in Destructive Weld Testing
Balancing Realism and Control:
One of the challenges in destructive testing is achieving a balance between realism and control. While the objective is to simulate real-world conditions, the test environment must remain controlled to yield meaningful results. Striking this balance requires meticulous planning and execution.
Cost and Resource Considerations:
Destructive testing consumes the welded material, making ita one-time evaluation. This can pose challenges in terms of cost and resource utilization. Therefore, strategic selection of samples and optimizing the testing process are essential considerations.
Conclusion: Preserving Integrity through Evaluation
In the intricate dance of welding, where the strength and resilience of joints are paramount, destructive weld testing emerges as a guardian of weld integrity. Far from being a mere destructive force, this testing methodology serves as a sentinel, ensuring that each weld is a testament to structural soundness. As industries continue to push the boundaries of materials and design, the role of destructive weld testing
remains indispensable—a guardian preserving the integrity of welds in
structures that shape our world.